Search
Aerospace
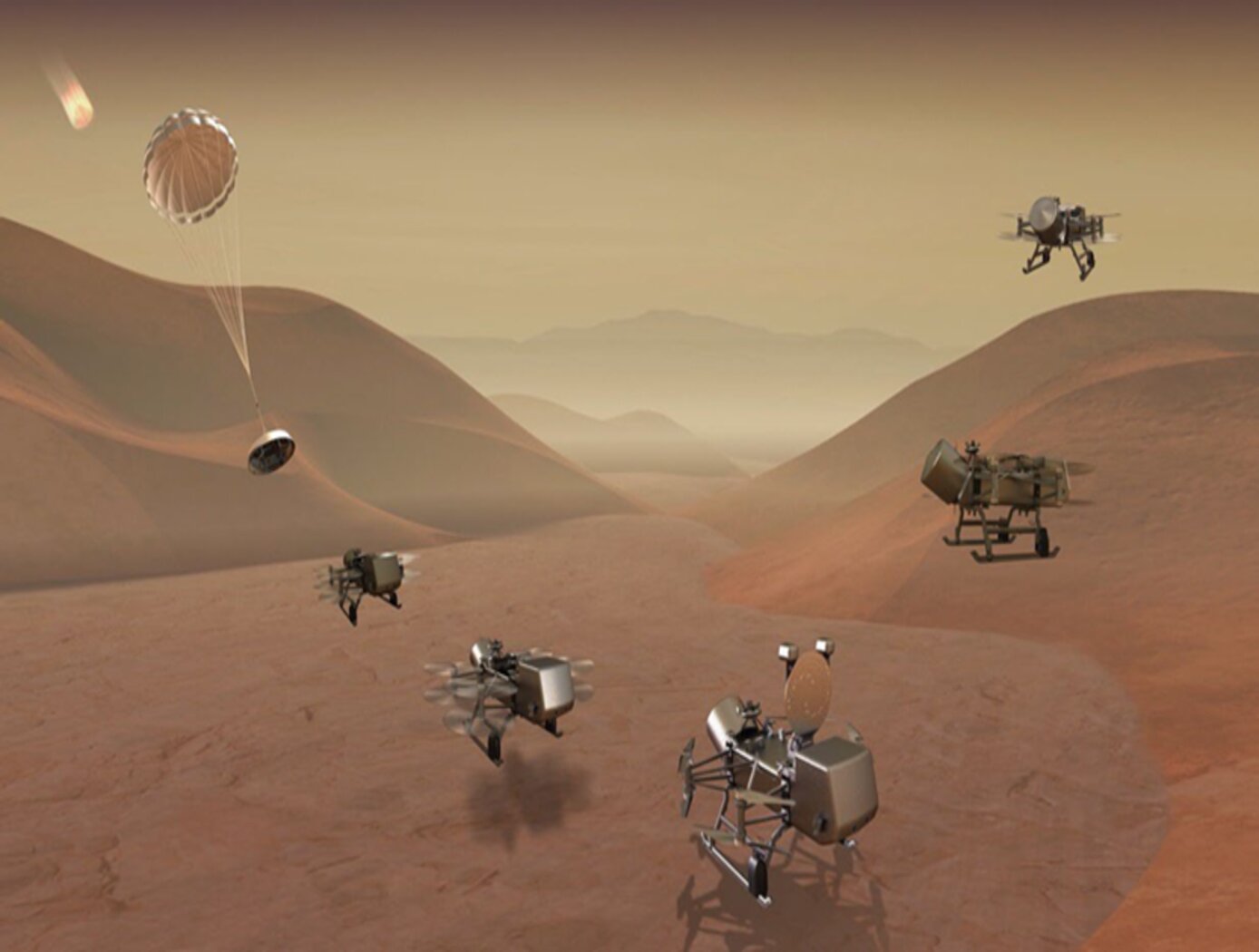
3D Lidar for Autonomous Landing Site Selection
Aerial planetary exploration spacecraft require lightweight, compact, and low power sensing systems to enable successful landing operations. The Ocellus 3D lidar meets those criteria as well as being able to withstand harsh planetary environments. Further, the new tool is based on space-qualified components and lidar technology previously developed at NASA Goddard (i.e., the Kodiak 3D lidar) as shown in the figure below.
The Ocellus 3D lidar quickly scans a near infrared laser across a planetary surface, receives that signal, and translates it into a 3D point cloud. Using a laser source, fast scanning MEMS (micro-electromechanical system)-based mirrors, and NASA-developed processing electronics, the 3D point clouds are created and converted into elevations and images onboard the craft. At ~2 km altitudes, Ocellus acts as an altimeter and at altitudes below 200 m the tool produces images and terrain maps. The produced high resolution (centimeter-scale) elevations are used by the spacecraft to assess safe landing sites.
The Ocellus 3D lidar is applicable to planetary and lunar exploration by unmanned or crewed aerial vehicles and may be adapted for assisting in-space servicing, assembly, and manufacturing operations. Beyond exploratory space missions, the new compact 3D lidar may be used for aerial navigation in the defense or commercial space sectors. The Ocellus 3D lidar is available for patent licensing.
instrumentation

RFID-Enabled Wireless Instrumentation
With a form factor close to a deck of playing cards, the system interrogator has custom software to interface with and service a population of sensor tags at the required data rates. Each EPCglobal C1G2 sensor tag uses incident interrogator energy to charge its small integrated circuit (IC), which reads an internal memory bank, encodes identification data, and uses that information to modulate and backscatter a reply to the interrogator using reflected interrogator energy. Two tag interfaces allow the attached processor to power the reading/writing of data to the tag memory and then allows the interrogator to power the reading of the tag memory data. When neither of the two interfaces are engaged, the RFID IC is completely powered down. Reading and writing tag memory consumes relatively little power compared to the power draw of active transmitter/receiver protocols like Bluetooth, Zigbee, and Wi-Fi. Compared to passive sensing protocols, this wireless instrumentation system enables sampling of a larger population of tags without the computational burden associated with surface acoustic wave (SAW) sensing. RFID-Enabled Wireless Instrumentation technology allows the RFID interrogator to write data through the interface of a sensor tag memory bank using only interrogator power. With only minimal cost to the sensors power budget, the microcontroller unit can read that data out over the serial interface. The sensor can transmit and receive data at no effective cost to its small coin cell battery power supply.
This technology is readiness level (TRL) 8 (actual system completed and "flight qualified" through test and demonstration) and the innovation is now available for your company to license. Please note that NASA does not manufacture products itself for commercial sale.